Case Study: Successful Implementation of Custom Material Handling Solutions
Introduction
In today's fast-paced industrial landscape, the need for efficient and customized material handling solutions has never been greater. Businesses are striving to optimize their operations and reduce costs while ensuring safety and productivity. This blog post delves into a successful case study illustrating how a company effectively implemented custom material handling solutions to achieve these goals.
Material handling is a crucial aspect of any manufacturing or distribution process. It involves the movement, protection, storage, and control of materials throughout the supply chain. Companies often face challenges related to inefficiencies, safety hazards, and high operational costs due to outdated or generic material handling systems.
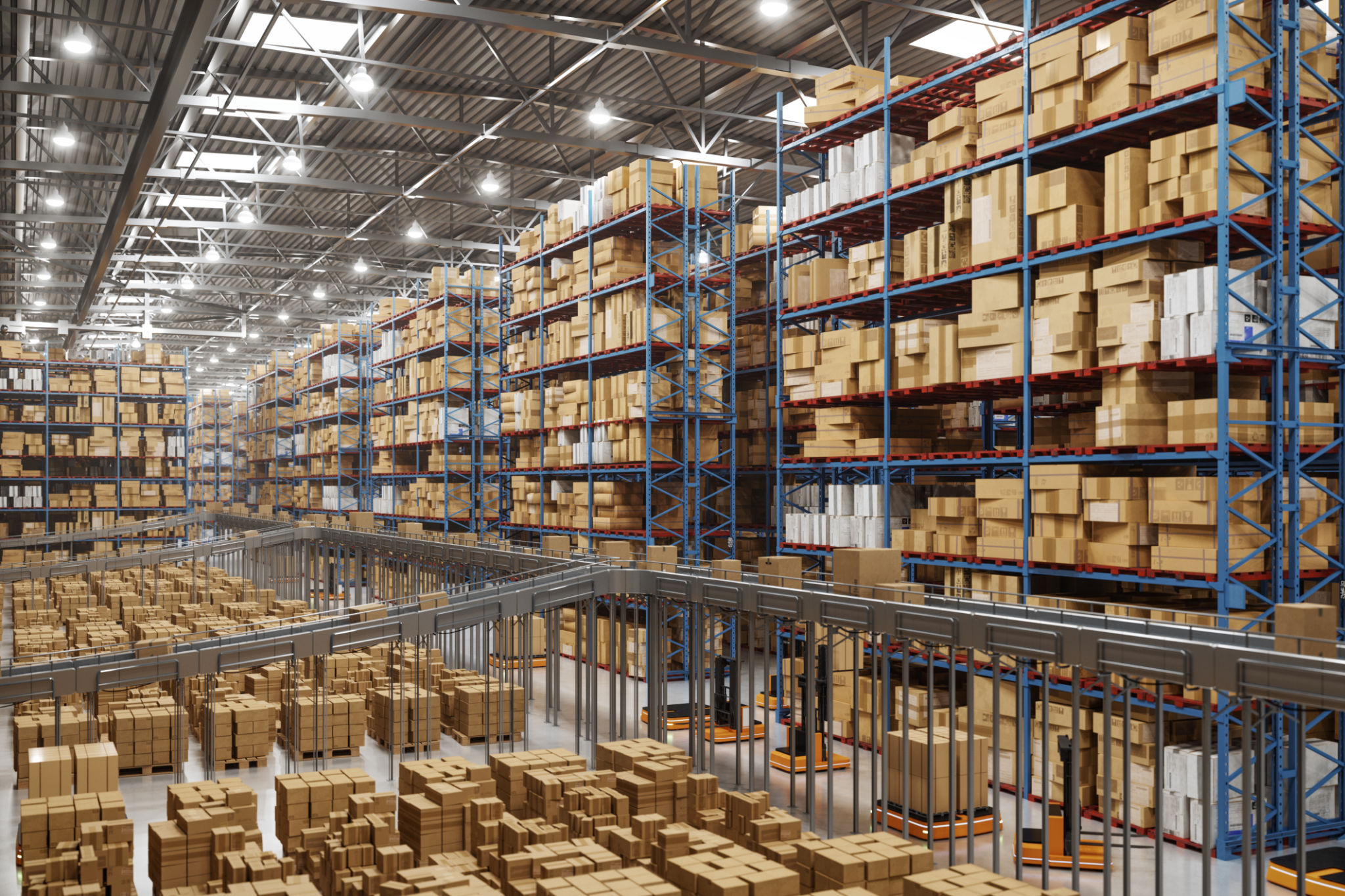
Identifying the Challenge
The company in focus, a leading manufacturer of automotive components, was experiencing significant bottlenecks in their production line. Their existing material handling system was not equipped to handle the increased volume and complexity of operations. This led to frequent delays, increased labor costs, and a higher risk of workplace injuries.
Upon conducting a thorough analysis, it became evident that a custom solution was required to address these specific challenges. The aim was to design a system that could streamline operations, enhance worker safety, and reduce overall costs.
Developing the Custom Solution
The company partnered with a renowned material handling solutions provider to develop a tailored system. The process began with an in-depth evaluation of the existing workflow, identifying key areas for improvement. The team then collaborated to design a solution that integrated seamlessly with the company's operations.
The custom solution included automated guided vehicles (AGVs) for efficient material transport, ergonomic workstations to minimize strain on workers, and an advanced warehouse management system (WMS) for real-time inventory tracking. These components were selected to ensure flexibility, scalability, and ease of use.

Implementation Process
Implementing the new material handling system was carried out in phases to minimize disruption. The first phase involved upgrading the existing infrastructure to support the new technology. This included installing sensors, conveyors, and other necessary equipment. Employees were trained on the new systems to ensure smooth operation.
The second phase focused on integrating the AGVs and WMS into daily operations. This required meticulous planning and coordination to ensure all components worked harmoniously together. Regular testing and feedback loops were established to refine the system further.
Results and Benefits
The implementation of custom material handling solutions yielded remarkable results. The company reported a 30% increase in production efficiency and a significant reduction in labor costs. The automated systems minimized human error, leading to improved product quality and consistency.

Moreover, the ergonomic improvements reduced workplace injuries by 40%, fostering a safer work environment. Employees experienced less fatigue and were able to focus on more value-added tasks, further enhancing productivity.
Long-term Impact
The success of this implementation has had a lasting impact on the company's operations. The scalability of the custom solutions allows for easy adaptation to future demands and technological advancements. As a result, the company is better positioned to meet market demands swiftly and efficiently.
This case study exemplifies the transformative power of custom material handling solutions in addressing industry-specific challenges. By investing in tailored systems, businesses can achieve operational excellence and remain competitive in today's ever-evolving market.